Yli 100 vuoden sitoutuminen tekniseen kehitykseen on tehnyt meistä johtavan valmistajan muuttuvien AC-taajuusmuuttajien, servokäyttöjen, ohjaustekniikan ja robotiikan aloilla.
Dosing with double screw pump
- Toimialat
- Elintarviketeollisuus
- Asiakasohjelma
- Fristam Pumpen KG
Precise Dosages and Powerful Cleaning in the Food Industry with Twin Screw Pumps
Twin screw pumps are classic process pumps and have proven themselves in countless applications. Up to now, however, they have been considered relatively unsuitable for precise dosing tasks. That is about to change. Thanks to powerful drive technology, they can now be operated in a way that stops the slippage between their feedscrews and enclosure from negatively affecting dosing results. Dripping – for instance, when filling bags with viscous media – is reliably prevented. This new development is especially beneficial for users whose systems are cleaned on a regular basis, because the cleaning processes involved are much simpler in comparison to those of piston pumps. Cleaning is much more efficient and frequent changes of product on the same filling system no longer pose a challenge.
Fristam Pumpen KG in Hamburg, Germany has grown into a renowned worldwide specialist for pumps for the widest variety of conveying tasks: from foodstuffs, to cosmetics and pharmaceuticals, to chemical applications. The company’s roots are in the dairy industry. No wonder, then, that these pump specialists have such a focus on applications with strict hygiene requirements. The twin screw pumps from the FDS series are an excellent example. They are made from high-quality stainless steel, easy to clean and are setting a multitude of new benchmarks in twin screw technology.
Higher Efficiency during Cleaning Processes
The functional principle has been completely revised from the ground up and known weak points have been eliminated. The design was continuously refined until every aspect was optimized, including smoothness of operation, temperature stability, repair and maintenance. “Furthermore, through these improvements we have managed to significantly increase the added value for end users by providing drive systems that are perfectly adapted to the pumps,” reports René Linck, Product Manager at Fristam. “The twin screw pumps are also now the ideal solution for dosing tasks with viscous or thixotropic media. At the same time, they can perform cleaning tasks in CIP processes at speeds of up to 3,600 min–1.” That means there is no need for an additional pump for cleaning processes. In comparison to piston pumps, which have generally been the standard pumps for such dosing tasks up to now, CIP processes run more quickly, especially since neither the pump nor the dosing hoses, pipes or nozzles have to be dismantled or removed. “That is especially beneficial in systems that need to be cleaned in short intervals because the product is changed frequently – for instance, if you use the same dosing unit to fill bags with ketchup in one shift and with mayonnaise or mustard in the next.”
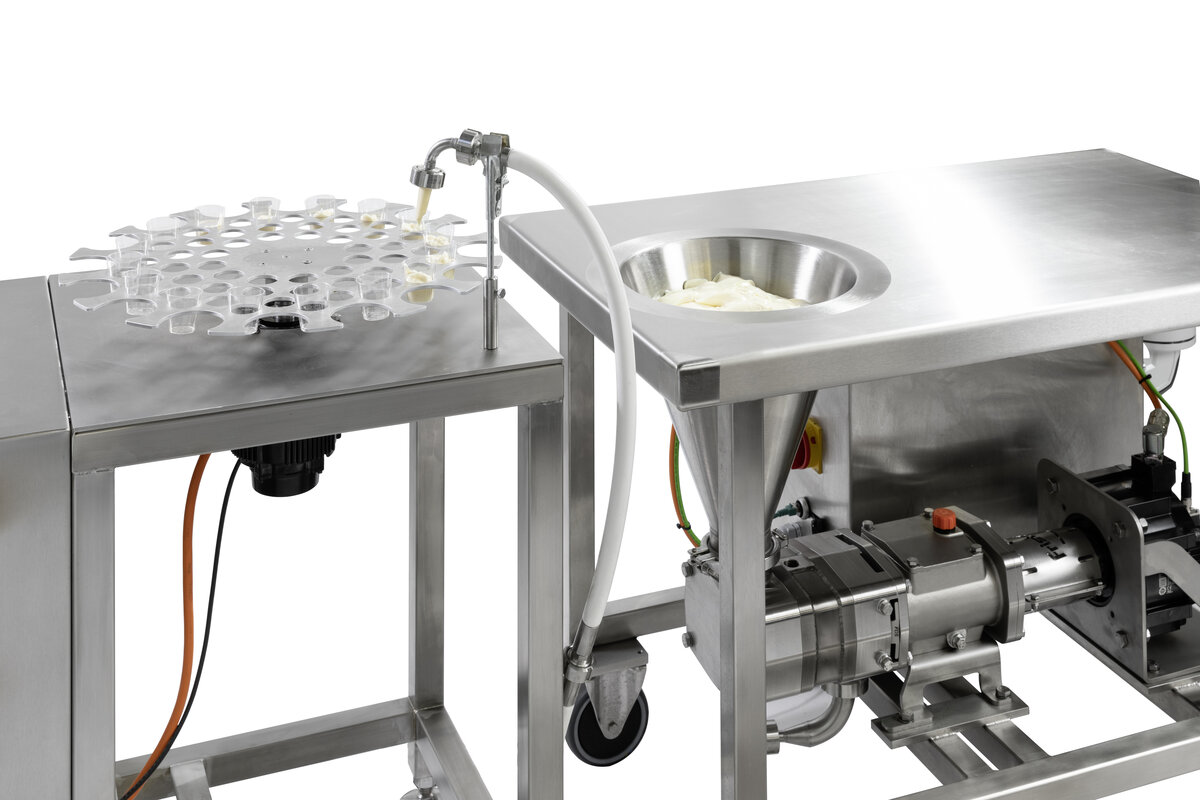
Drive Engineering Challenge
The challenge during development was to prevent dripping while filling bags. The slippage between the screws and the interior wall of the housing is inherent to the design and cannot be prevented. A certain spacing must always be ensured so that the non-contact pump functions correctly and the surface of the screws and housing are not damaged. To seal the screws for the compressors, for instance, the gap is sealed with an injection lubrication. In twin screw pumps, the conveyed medium performs this task itself. However, this results in the “slippage” described above. Depending on the viscosity of the medium, the volume conveyed differs with each revolution. Twin screw pumps offer an elegant solution to this problem: The sensitive yet highly dynamic drive system prevents any dripping. To do that, the pump drive briefly runs backwards for a specific time at the end of the filling process, ensuring a precise dosage and a clean filling process.
This is a challenging task for the drive solution used, because each different kind of media requires adapted acceleration, braking and return ramps. In addition to this, the cycle times are short because the pumps fill up to 80 bags per minute. High dynamism is therefore crucial. “In close collaboration with Yaskawa, a partner of ours for many years, we managed to create a drive solution adapted perfectly to these requirements,” reports Linck happily.
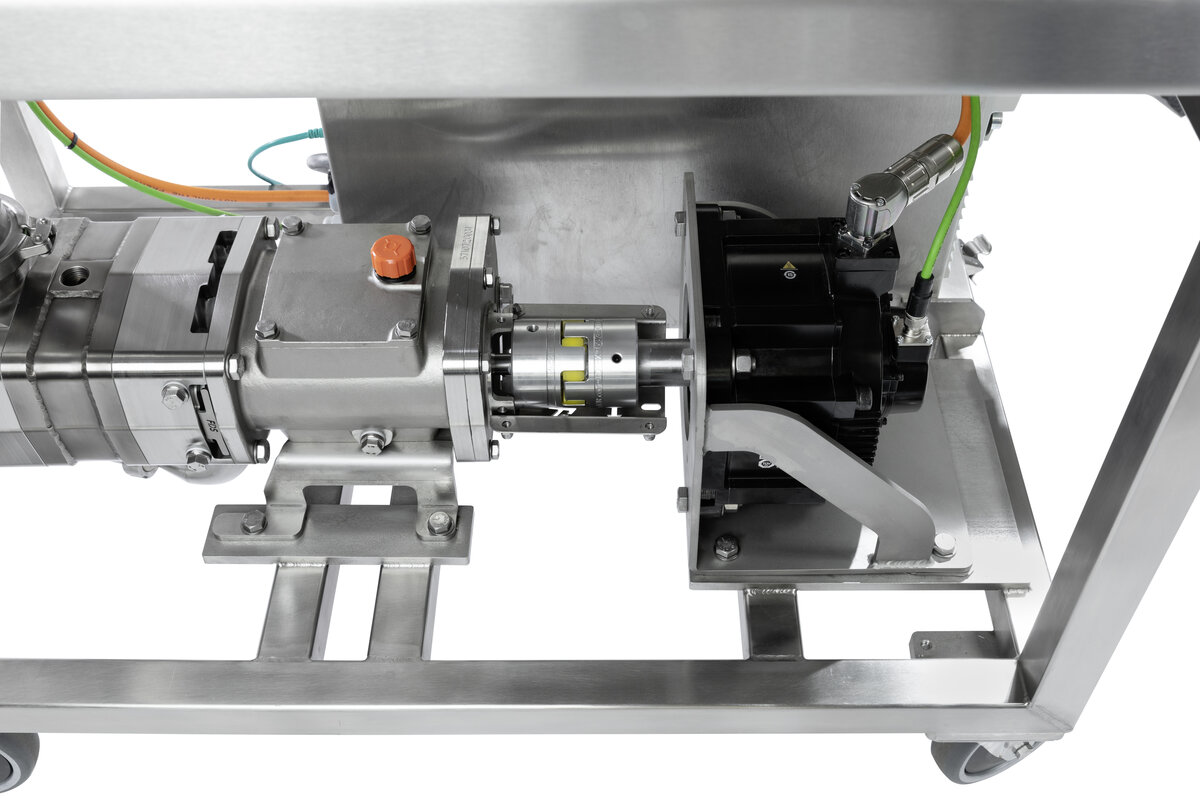
Complete Drive Train from One Single Source
The driving force for the twin screw pumps is provided by Sigma 7 servo motors and the appropriate amplifiers. The rapid-response AC servo drives feature a high resolution (integrated 24-bit absolute encoder) and high dynamism, and are ideal for demanding positioning tasks. They are capable of suppressing vibrations and machine resonance frequencies automatically during operation. They are also designed for a long service life and operate at ambient temperatures of between 0 and 55° C without additional cooling. Thanks to their compact dimensions, they require only a small installation space and are easy to mount on dosing units that are commonly used on the rotary tables in filling systems. There was also a large range to choose from during project planning. The highly dynamic AC servo motors cover outputs from 50 W to 15 kW at supply voltages of 200 and 400 V, and are impressively quiet when running.
A compact Yaskawa control system from the VIPA SLIO series controls the servo axis for the dosing work. This system is easy to program in Siemens Step7 and its modular design means it can be adapted well to the application. For convenient control over the dosing process, the Yaskawa controller was fitted with a smart HMI. Its 7 inch display not only enables menu-guided operation, but also lets you visualize the dosing unit. The combination of high-quality components and expert personal support while adapting the solutions to the specific requirements made Yaskawa the perfect partner. “We got a complete functional solution for our dosing unit from one single source,” beams Linck.
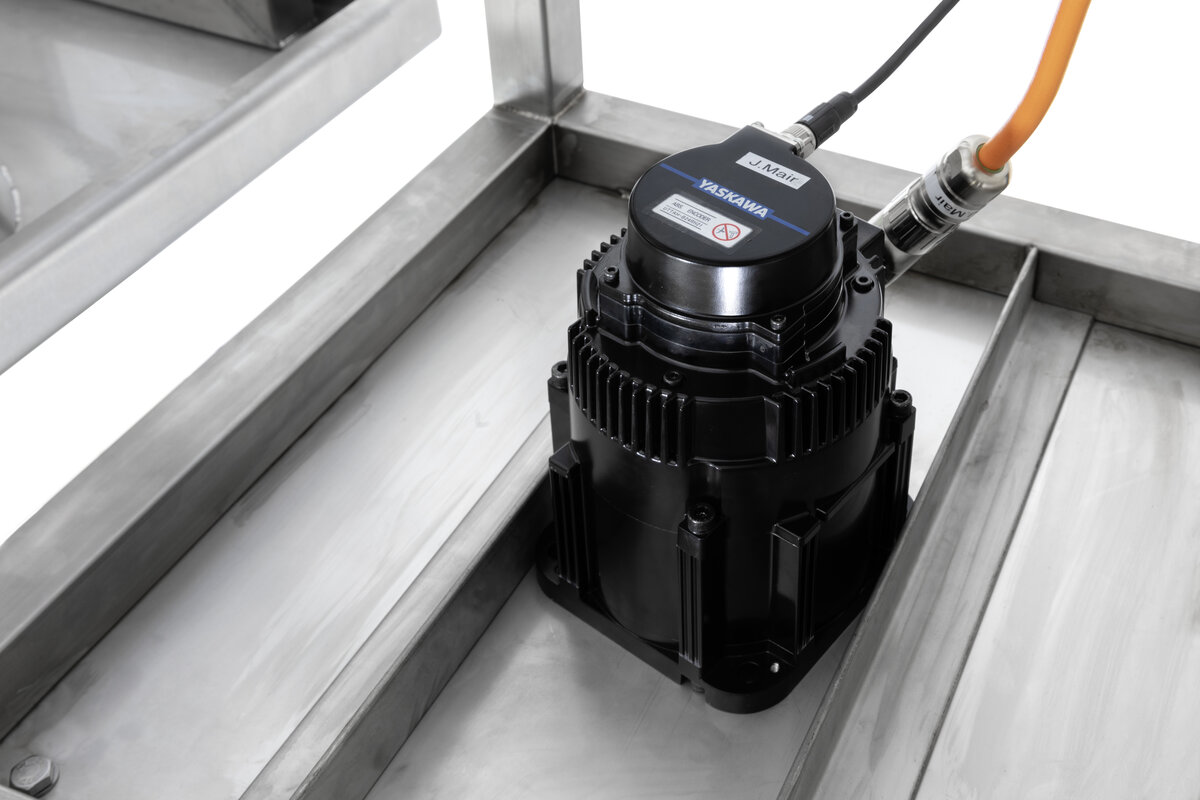