Yli 100 vuoden sitoutuminen tekniseen kehitykseen on tehnyt meistä johtavan valmistajan muuttuvien AC-taajuusmuuttajien, servokäyttöjen, ohjaustekniikan ja robotiikan aloilla.
In the service of beauty
Challenge
Higher energy efficiency at L’Oréal in Karlsruhe/Germany
The cosmetics group L’Oréal has defined environmental protection as an important corporate objective. This goal will not only be implemented in the production process but also in building automation. At their location in Karlsruhe the heating system has now been modernized – with savings and solutions from Yaskawa.
The name L’Oréal stands for cosmetics, and hair and skincare worldwide. For Germany and parts of Europe, the consumer brands, L’Oréal Paris and Garnier, are produced in Karlsruhe, the only German production center of the group. The high ethical principles of this global player are remarkable. Besides other aspects, L’Oréal pays attention to water and energy consumption. Nearly all factories have an emission permit in accordance with ISO 14001 and a safety certificate in accordance with OHSAS 18000 or OSHA VPP.
Consequently, also in building technology, the company places a great deal of emphasis on sustainability and energy efficiency. The existing heating was replaced with district heating and a new controller. Because they had already managed several joint projects successfully, the company Khim Automation, from nearby Hambrücken, was also to manage the control and automation engineering at L’Oréal.
Solution
Specialists rely on PLC engineering
Khim has specialized in technical building automation and HVAC (heating/ventilating/air conditioning) systems, whereby the focus is on energy controlling, savings, and networked systems. As the conversion had to be completed during operation – also at the weekends – one area after another was modernized according to the requirements of production. So after three months the heating in the production was completely converted.
There were several reasons for Khim to rely here on PLC engineering instead of on systems such as BACnet, KNX or LON which are usually used in building technology. PLC engineering can be found everywhere in the industry and there is staff there who are very familiar with it. Spare parts are in-house and the customer can mostly deal with faults or changes himself without any delay. In addition, the STEP7 compatibility, the interfaces to PROFIBUS, and the performance capability of the CPU to process and reliably store large amounts of data spoke for Yaskawa and their Vipa SPEED7 CPUs. All required interfaces are on board with Vipa CPUs as standard, and the capacity is sufficient to process the 90 parameters which accrue per control module in this project.
Two CPUs 315SN-NET control the entire energy distribution – together with decentralized SLIO modules Two CPUs of the type 315-4NE12 Ethernet now control the right temperature of the entire building in Karlsruhe. 18 Vipa SLIO module units are connected decentralized over the entire factory on 4.5 km of Profibus cable, strengthened by repeaters. They control the energy distribution on-site and ensure that the return per consumption unit does not rise above the desired value – otherwise the amount is throttled.
Result
Expectations exceeded
The success of the modernization has exceeded all expectations. It was possible to reduce heating costs significantly, thereby further promoting the company’s goal of sustainability.
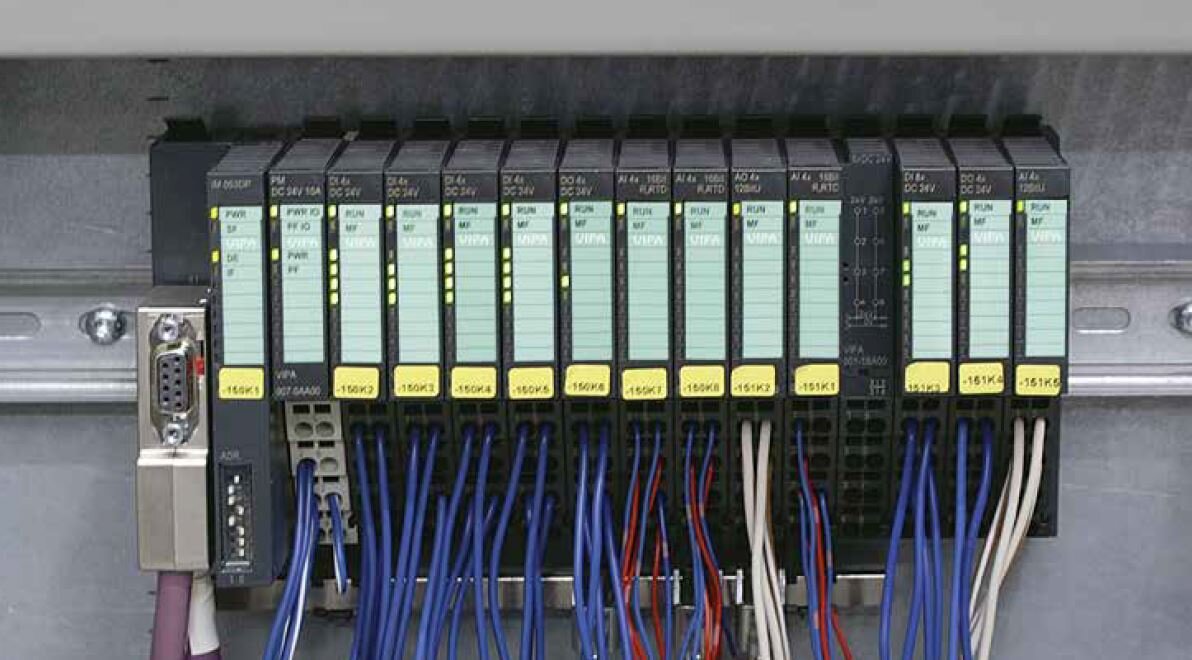